There is not a bigger vicious cycle in this world than that of problems which constantly re-occur because there is no time to stop and solve them correctly.
Although we all would like for this cycle to stop, Managers can’t afford letting employees waste time with too much researching and employees don’t have the time because they are constantly fighting fires. As long as this cycle continues, problems will reoccur and everyone will have to spend more time in what should not have occurred on the first place. How do we get out of this vicious cycle? Through training, dedication and appropriate problem solving techniques.
Why are we always fighting fires?
Is no doubt that time is more than a precious stone, it is not only valuable but once it is gone there is no way to get it back, no matter how much we are willing to pay. At work, time is even more valuable, as we only have 8 hours a day to be productive and achieve our daily tasks and goals. Although we are all well intended, somehow time at work just seems to go by too fast. Between reading emails and fighting fires, the work day is gone and there is no time to look at the big picture or even think of improvements. But why are we fighting fires on the first place?
If you look at every problem that causes us to stop everything we are doing and dedicate our resources to that problem, chances are you will say that the problem should not have occurred. Not only should the problem not have occurred, but it could have been prevented, very easily. Or furthermore, you could even say that the problem already happened, and therefore there was no reason why it should have happened again. But somehow, somewhere, something broke and all of the sudden the problem resurfaced.
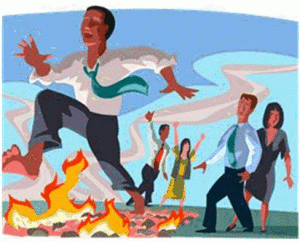
But usually there is no time to ponder. You don’t want to look as if you are not acting or doing something about the problem and therefore you put on your firefighter outfit and go fight the fire along with everyone else. Fortunately you may think, all those fighting the fire are equally smart like you and whether you were there when the problem occurred, you feel that the most intelligent people in the company are the ones putting the problem and the fire down. Little do we know that the smarter people in the company are not always the only people who should be solving the issue, but, is another issue out of many and there is no time to sit and think of other ways to do it, because the problem is critical and we better take care of it because tomorrow we may have another fire and because we don’t want to look as if we haven’t done enough already.
But the problem is not so much in the fire or the people who caused it, but rather the system who allowed it to happen.
Where is the system?
When I look at organizations that are constantly in fire fighting mode, I see that there is not a system in place to allow improving from mistakes. Either mistakes are not recognized as such, or the organization views mistakes and errors as a detriment to the organization. Employees are scare of bringing problems or potential problems to management’s attention in fear of reprisal. Management sees problems as Operator error and considers every problem an opportunity for reorganization. A system of proper root cause analysis is unknown and problem solving is usually handled by a selected few. A lack of a Problem Solving and Continual Improvement system prevents the organization from using those “errors, problems or mistakes” as valuable tools to improve its processes.
Basically, for re-current problems to stop from re-appearing, a system is needed where the vicious cycle cannot be allowed to happen. That can only be achieved when there is a system in place that allows for the following three elements to exist:
- Company-wide training in Root Cause Analysis Techniques and Problem Solving.
- Commitment from the organization leadership to continual improvement.
- A robust yet simple process for conducting Corrective or Preventive actions that includes all elements of a proper Root Cause Analysis and Problem Solving.
Without the 3 elements above, a process for stopping problems from happening again will not exist or will not be able to be sustained over time. These 3 elements ensure that the system in the organization is conducive to continual improvement and that appropriate root cause analysis and problem solving will prevent problems from re-occurring.
Company Wide Training is Essential
Training in Root Causes Analysis and Problem Solving is a basic requirement if you want your organization to move away from fire fighting mode. However training must occur throughout the organization, not just for a few manager or the company auditors. It is imperative that from the top executives of the organization all the way to the floor shop employees or desk clerks, everyone be trained on these techniques.
An organization may be surprised how much they are losing by depriving their employees from these essential tools. As a consultant and auditor, I see this all the time. Employees thinking they have close out issues, only to find out they were closed on paper, not in real life. After many of these encounters, I have come to believe that is not that they forgot to complete their actions or that somebody misinterpret them, is just that they do not understand the concepts of problem solving. Some people literally think that a problem is solved when you have stated what you are planning to do to solve the problem, while others think that a problem is solved when the specific issue that caused the nonconformity is resolved. Yet others think that problems never really happen and the fire fighting status quo is the norm.
Training is therefore essential to ensuring that everyone understands the process from finding the root causes of the problem and ensuring that the problem does not happen again. In reality, a problem is not resolved when the root cause analysis has been conducted. There are events that must happen before and after in order from the problem to be fully resolved and not re-occur. Activities like containment, notification, design, mistake proofing, verification, etc. are all part of solving a problem properly. Of course not all problems are created equal, and therefore employees must be trained adequately in order to understand how to apply the simple problem solving techniques to their everyday problems and challenges.
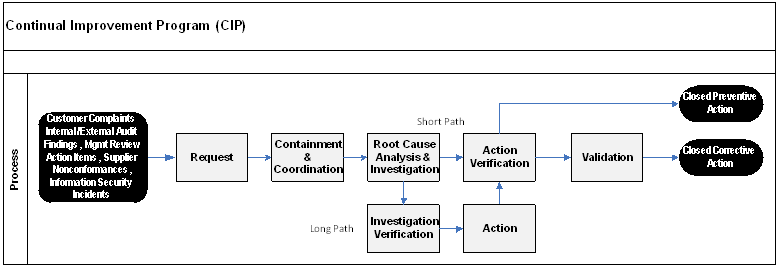
Equally important is to train top management in the root cause analysis and problem solving techniques. I get puzzled when a manager asks for a problem to be solved correctly yet demands immediate action and not too much investigation: “More doing and less talking”, may be a familiar phrase. While we all want to minimize unproductive time, it is necessary that Management understand problem solving techniques so that they can understand that the depth of activities necessary to solve a problem are commensurable to the problem in question and the need to stop the problem from happening again. A return from a customer is a problem that can be easily solved by giving the customer credit back, however to stop that problem from happening again requires a lot more than that.
And because problems happen at all levels of the organization, everyone must be trained.
Leadership Commitment
I would like to think that once the management of an organization has been trained in Root Cause Analysis and Problem Solving techniques, they will be more apt to giving employees the time as well as the resources they need to solve a problem. Problems vary and so does the effort and time allocated to solved them properly. When management understand these concepts and techniques, they will understand than giving a customer credit back is like putting a band aid to a wound: it will not solve the issue of why the wound happened on the first place. Nor would a simple problem solving session be able to capitalize on the lessons learned and cross pollinate within an organization’s multiple locations. For that to happen you need time and you need management to be committed to giving that time and allowing all the appropriate manpower resources to share those lessons.
We understand that financial resources are not always available, but well trained employees will learn the proper techniques to find alternative solutions to solve problems, to implement mistake proof systems that may not necessarily be more costly and that may in fact save money. After all, when a problem reoccurs, you are already wasted time, resources and money time and again. Therefore allowing your employees to work on continually improving the system not only saves you time and money but also helps your company improve.
Keep it Simple and Robust…Your corrective and preventive action system
Usually your corrective and preventive action system should be the one where the entire root cause analysis and problem solving is done. Thus, I cannot stress enough that your corrective and preventive action system must be designed with continual improvement in mind, and therefore all your employees should have equal rights to it. You cannot expect employees to use the system for solving problems, when it is not accessible to them or when it is too cumbersome to use.
Likewise you cannot have a corrective and preventive action system that is disjoint or that does not encourage employees to think about containment, root causes analysis and verification for example. The entire system of problem solving should be embedded in your corrective and preventive action system, so that there are no other systems out there duplicating efforts. Moreover, management must believe in the system, encourage its use and use it themselves. This will create a sense of trust in the system that employees will see and therefore follow.
Finally, your corrective and preventive action system must be designed so that anyone who has encountered a problem or a potential problem feels empower to bring it up to management’s attention. The system should also be simple enough for everyone to follow and robust so that you don’t have to hire extra people just to maintain the system. The idea is that whatever paper or electronic tool you use, it must be easy to maintain and sustain.
So is it going to be 1 or 8 hours?
So now that you understand what is needed to stop firefighting and foster an organization that values continual improvement, are you ready to dedicate 1 hour of your day to it?

This article was published by Quality Digest on 03/11/2011.