When you think about equipment that is used for measuring and test activities, you think about important equipment that is used to pass/fail product but may not necessarily find correlation with suppliers. However this very equipment – whether is calibrated in-house or off-site – does involve a supply chain one way or the other and therefore adherence to suppliers and supply-chain requirements is imperative.
If you outsource your calibration, you know that your calibration partners are your vendors. But when equipment is calibrated in-house you may think there are not suppliers involved, however in this case, you probably still have to send “the standard” used for calibration, to an outside calibration company that can provide traceability to NIST standards. So whether the calibration is done in-house or by an external company, calibration does involve a look into your purchasing procedures and your supply chain.
Supply Chain
When you send equipment out for calibration, the calibrating company becomes your supplier and is therefore subject to all the controls set forth in your supply chain or supplier approval procedures. If your procedure is laid out correctly, then you will find most of the controls familiar. In fact, if you segregate your suppliers, in most cases calibration companies will fall under your top tier or critical suppliers because you depend on them, to calibrate your equipment that will actually determine the quality of your product. Since the equipment you use will actually pass or fail your product, you want to make sure the companies who calibrate your equipment are good, reputable suppliers.
The first thing you want to make sure is that the calibration company or companies you used are part of your approved supplier list (ASL) or approved vendor list (AVL). Unless they were grandfathered –that is those suppliers existed before you put in place your supply chain approval procedures- then you need to be able to demonstrate that the calibration companies were approved following your calibration procedures. For example if you require that all your prospect suppliers fill out a survey before approval, then you should have one on hand for your calibration suppliers. Likewise if you require ISO 17025 or ISO 9001 certificate in lieu of survey or on-site audit as a method for approval, then you should have that on-hand if the survey is not available. Whether you need to get busy now and fill out a survey or request for documents, you must ensure that the current calibration suppliers meet all the requirements set forth in your procedures.
“You must ensure that the current calibration suppliers meet all the requirements set forth in your procedures.”
The ISO 9001 standard requires that suppliers be re-evaluated and you should have a process already in place for that. Since your calibration partners are suppliers, then you have to make sure you re-evaluate them using the same procedures, whether than entails periodic audits, periodic surveys, SCAR or corrective action statistics, etc. If you feel that the current process in place is too cumbersome or not adequate for your calibration suppliers, you should modify your process and corresponding procedures to accommodate for them. The idea is to make sure that these companies are subject to the supply chain requirements and that there are records to prove they are meeting those requirements.
Purchasing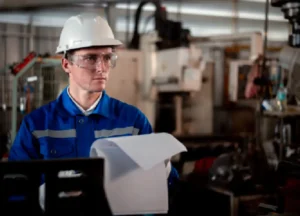
Believe it or not, when you send equipment out for calibration you are in a way outsourcing your calibration process, and therefore you need to apply extensive controls to your calibration partners to ensure that they are performing the assigned duties based on your requirements.
One of the main steps when Purchasing issues purchase orders to the calibrating company is to make sure that those purchases establish the requirements for how you want the calibration to be done. For example some companies issue purchase orders with reference to their internal calibration procedures. Other may specify on the purchase order the parameters required to calibrate the equipment, such as:
- Methods or protocol
- Accuracy and tolerance
- Items to include in calibration certificate, etc.
If the accuracy, tolerances, method, etc. is contained within your procedure, then you need only reference that procedure. Otherwise, you need to convey to the calibration company how you want this equipment to be calibrated. If you require calibration according to a procedure, then you should either email the procedure, attach it to the purchase order, etc.
You also have to pay close attention on the revision dates. For example if you issued a purchase order last year to a calibration company and referenced your calibration procedure dated last year, that was great for last year. But if you issue a purchase order this year, you should now see if there is a new revision of the procedure and ensure that the Calibration partner has that particular version. Some companies adopt a blanket statement such as:
“Calibrate to the latest revision of procedure ABC-XXX”
If you follow this statement, then you have to discuss with your calibration partner to make sure they read your purchase order and always request the latest copy of ABC-XXX -if you do not automatically provide one to them every time you update such procedure. So whichever way you go, your Purchasing group, your Supply Chain group and your calibration vendor have to be knowledgeable of what is required and expected of them.
Maintaining control
Overall control over your Calibration partners is necessary to ensure they are meeting your requirements. Just telling them you want a piece of equipment to be calibrated is not sufficient. Likewise, assuming your Purchasing department –Supply Chain group, Logistics, etc. – know and understand their requirements, is not prudent, so be certain they recognize the implications of dealing with and ordering from calibration suppliers. With good processes and procedures in place, and thorough training, you should expect excellent results in your calibration purchases and ultimately be confident that your product and processes are being inspected and tested with fully compliant equipment.
This article was published by Quality Digest on 10/05/2009.
Get Help with Your API or ISO Audit from MireauxMS
Whether you need a gap analysis, pre-audit preparation, or full audit support, our team is ready to guide you through every step. We bring years of hands-on experience with ISO and API standards to help you achieve compliance with confidence.ISO Audits
API Audits