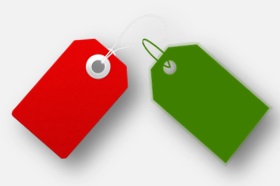
When it comes to red tags and green tags, which does your company use?
A reader shared this material identification issue with us after a recent audit: “Our process for material identification requires that we identify the material with a green tag (it’s good to go) or a red tag (stop, there is an issue).
We then attach a green tag with the processed order. Sometimes, what happens is we will order material, which we will have in stock (not necessarily tied to a customer PO) until it becomes inventory. How do we identify the material throughout the process when that inventory (already green tagged) becomes raw material for another Client?”
Stay Compliant For Your Next Audit
We think the green/red tags should still carry over. Let’s say you have a whole piece of sheet metal, and cut a quarter of it; is the remaining sheet metal good or bad? As long as you update the green tag, perhaps, or ensure that the Material Test Reports (MTRs) are still attached, this material should be considered “good to go.” Say you lose the MTR, or you do not know the heat code, or even if you simply bump the material, you may have to inspect and retest the material before it is good to go. In this case, you will have to red tag the material for the time being. Whether for ISO 9001, API Q1 9th Edition, API Q2 or another standard, this will ensure that you are compliant for your next audit.